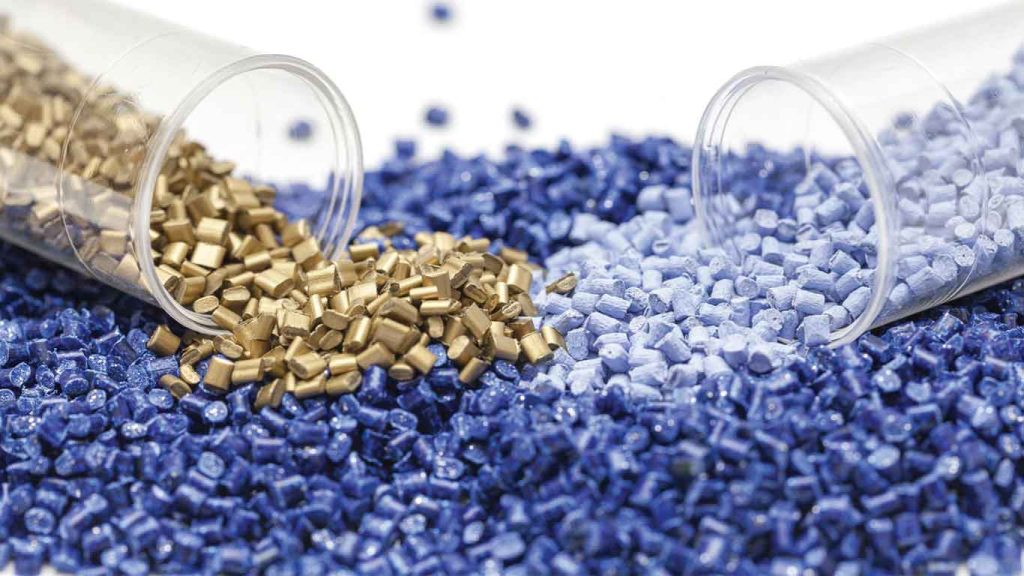
The name granule is probably heard by most people in the plastics and polymer industry. The story began with the advancement of technology, various methods and devices for the production of plastic products, and the question arose as to what the raw material used in these devices would be. Among powder forms, granules and flakes, granules have won this competition due to their many advantages, and in most production methods, granules are used as a raw material to produce the final product. But what is granule and what are its benefits? What types are there? How is it produced? If you have similar questions in your mind, join us in this article to get the answers to your questions.
What is granule?
The misconception that granules have in the minds of some people who are a little unfamiliar with the field of polymers and plastics is that this product is a kind of polymeric material. As the first and most important point, you should know that granules are not the name of a specific polymer and are a form of polymer that is in powder form in the form of granules (as in the picture below) and is used in various applications and applications.
The reason for using granules is the ease of use in production; The powders are dispersed in the air and in addition to the pollution of the workshop environment and the respiratory problems they cause, a large amount of material is wasted, but the granules do not have these problems. In addition, the system of plastic forming machines is designed in such a way that its raw materials are in the form of granules. Therefore, manufacturers prefer to use its granular form instead of powder. To produce polymer products from granules, it must first be melted and then molded.
Division of granule types
Granules are in most cases the final product by the two common methods of injection molding and pneumatic molding (not to mention the rotary molding method, of course). Depending on the crystal structure of the raw material and the production methods, different classifications of granules are formed. Among the most important and widely used granules, we can mention polyethylene granules (and its grades) and polypropylene granules (and its grades).
Polyethylene granules
Polyethylene granules have a specific crystal structure and chemical formula. By changing the arrangement of polymer branches in polyethylene, light, medium, heavy and very high molecular weight grades are formed. Depending on the production methods, polyethylenes can be divided into injection grade or pneumatic. By combining these two classification methods, the most important grades of polyethylene include the following categories:
Injectable light granules
Heavy injection granules
Heavy pneumatic granules
Linear lightweight polyethylene granules
Of course, there are other grades that are only mentioned here in the more common categories. For example, injectable heavy polyethylene granules are firstly granules whose structure and composition are light and secondly used in injection molding methods.
Polypropylene granules
This article is generally divided into two categories:
Homopolymer, which is produced by the polymerization of propylene monomer alone, is also called textile PP.
A copolymer produced by the polymerization of propylene with an ethylene commonomer is also called chemical PP.
Polycarbonate granules
Polycarbonate is a type of transparent polymer that is used in the manufacture of various devices. Transparency and the possibility of light transmission are the most important features of polycarbonate. Injectable polycarbonate is used to produce products such as car headlights, plastic parts for home appliances, medical equipment, consumer products, and more. One of the disadvantages of this granule is its high cracking ability.
Other common granules
In addition to the above, there are other types of granules that are used in various applications. These materials include polystyrene, ABS, engineering polymers and other granules.
Important points you should know about polymer granules!
All polymeric materials can be granulated depending on the application, the degree of viscosity and other factors such as the type of polymerization and.. However, if the polymerization conditions and other factors are complex, the polymer is produced as a powder or solution or.. The main purpose of producing a polymer is to obtain a material with the desired properties. Obtaining these properties and controlling them during the polymerization process depends on many factors such as temperature, pressure, catalyst and…. has it. Polymer that is first melted and molded certainly has better properties than recycled polymers. Some polymers retain their properties after melting and forming several times. But some of them, such as PVC, which are widely used in door and window profiles, tablecloths and sheets, cables, appliances, etc., lose their properties after recycling.
One of the most widespread and important sectors of the plastics industry is the recycling of plastic waste into reusable granules for other manufacturers, because the raw materials of this industry are worn and coated rubbers in the country, which are found in abundance in Iran and several annually. A thousand tons are added to their volume.
Also, the product produced by these machines – standard rubber powder and granules – is the raw material of many industries such as the production of various types of flooring, all kinds of reinforcements and alternatives in paints, asphalt, concrete, as well as the main fuel of the furnace, rubber raw material and application. It has many inside and outside the country. To read more about this, you can refer to the article on recycled granules.
Granule production
To produce the granule, when the polymer is produced, it is melted in the extruder (something like a meat grinder) and a cutter or something similar is installed in the head of the extruder, which cuts the output polymer regularly and produces the granule.
Recycled plastic materials that have milled shapes and sharp shapes or corners can not be easily used in the input hoppers of these devices, and of course the mixing time due to their non-uniform size with other materials always have a non-uniform composition. Therefore, consumers of these materials prefer the materials they buy like materials